With an e-commerce WMS, retailers can maximize their growth potential. Photo: Descartes
Commercial collaboration
In today’s fast-paced online marketplace, achieving operational excellence in warehouse logistics is not simply an operational tweak – it is a strategic necessity. With customer expectations for lightning-fast, error-free deliveries at an all-time high, modern ecommerce companies must adopt digital tools that streamline and scale their fulfillment processes. A robust ecommerce warehouse management system (WMS) can transform a company’s backend operations, ensuring that every order is processed quickly and accurately while supporting rapid growth.
This article delves into the challenges faced by growing ecommerce businesses, explains how an advanced WMS can empower brands to overcome these obstacles, and offers a roadmap for selecting and implementing the ideal solution.
The growing complexity of Ecommerce warehouse logistics
Surging order volumes and seasonal peaks
The nature of ecommerce is such that order volumes can fluctuate wildly. Social media campaigns, product launches, flash sales, and seasonal shopping events – like Black Friday or back-to-school periods – can lead to sudden and dramatic increases in orders. For many businesses, these peaks present several challenges:
- Order Fulfillment Bottlenecks: When order numbers spike, manual processes quickly become overwhelmed. Inefficient picking routes and poorly optimized batching can slow fulfillment times and hinder overall performance.
- Inventory Inaccuracies: Without real-time tracking, businesses risk overselling products or depleting stocks unexpectedly, leading to customer dissatisfaction and costly operational disruptions.
- Increased Labor Costs: Relying on manual processes often necessitates hiring temporary staff to manage peak loads, which can escalate labor expenses and complicate workforce management.
- Returns Management Complexities: Handling returns – an increasingly critical part of the customer experience – can become cumbersome if not properly integrated into the order lifecycle.
The imperative of digital transformation
Traditional manual systems and legacy software often cannot keep pace with the rapid growth and complexity of today’s ecommerce operations. The solution lies in a comprehensive digital transformation that automates and optimizes every step of the fulfillment process. By integrating a state-of-the-art WMS, retailers can drastically reduce manual intervention, boost operational efficiency, and maintain high levels of accuracy even during peak demand periods.
Empowering growth with an advanced Ecommerce WMS
A modern ecommerce WMS leverages automation, real-time data, and intelligent process design to address many of the challenges discussed above. Here’s how these systems empower fast-growing brands:
1. Streamlined Order Fulfillment and Accelerated Shipping
At the heart of any successful ecommerce operation is the ability to fulfill orders swiftly and accurately. An advanced WMS optimizes the entire fulfillment process through several key features:
- Mobile-Driven Multi-Order Picking: Workers equipped with mobile devices can scan barcodes and rapidly locate items. This minimizes the time spent searching for products and reduces the risk of picking errors.
- Intelligent Order Batching: Orders are grouped based on shared attributes – such as destination or delivery speed requirements – allowing staff to efficiently pick multiple orders in one pass.
- Optimized Pick Paths: Advanced algorithms determine the most efficient routes through the warehouse, ensuring that every movement is purposeful and time-saving.
During periods of high demand, these automated processes enable a company to maintain or even shorten shipping times, ensuring that orders are dispatched on the same day and customers remain satisfied.
2. Real-Time Inventory Accuracy and Enhanced Stock Visibility
One of the primary benefits of an integrated WMS is its ability to maintain accurate, real-time inventory levels across all sales channels. This ensures that:
- Stock Replenishment Is Automated: The system continuously monitors inventory levels and triggers alerts for replenishment, preventing stockouts and overselling.
- Barcode Technologies Minimize Errors: Automated scanning processes significantly reduce human errors during both the receiving and storage phases.
- A Centralized Data Hub Maintains Consistency: By consolidating all inventory data in real time, the WMS creates a single source of truth that is accessible to the entire organization.
This level of visibility is essential for making informed decisions and ensuring that customer orders are always fulfilled based on accurate stock information while overselling is being avoided.
3. Scalability to Handle Fluctuating Demand
Fast-growing ecommerce businesses require solutions that can scale seamlessly with their operations. A flexible WMS addresses this need by offering:
- Dynamic Warehouse Layouts: Modern systems often support “chaotic warehousing,” a flexible storage method that maximizes warehouse space utilization by using available empty storage locations rather than fixed locations.
- Multi-Warehouse Management: For brands operating from multiple locations, the ability to manage all warehouses from a single, centralized platform is invaluable. This capability allows for coordinated inventory management and effective order distribution across regions.
- Rapid Onboarding and Integration: With implementation timelines as short as 6-12 weeks, a modern WMS can be deployed quickly and integrated with existing systems, ensuring that businesses can adapt to rising demand without experiencing operational delays.
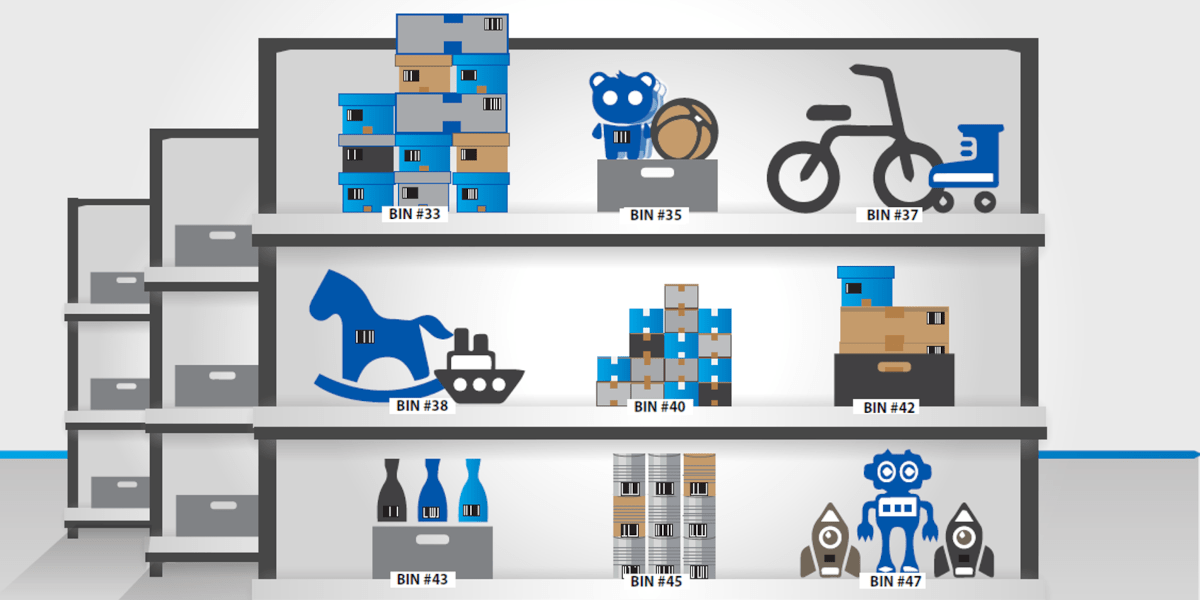
4. Minimization of Human Error Through Process Automation
Reducing human error is critical to maintaining operational efficiency and ensuring customer satisfaction. An effective WMS minimizes mistakes by automating repetitive tasks:
- Barcode Scanning Enhances Accuracy: Automated scanning confirms that the correct items are picked and packed, reducing the likelihood of order errors.
- Automated Documentation: Packing slips, shipping labels, and other documentation are generated automatically, reducing the potential for manual errors.
- Smart Routing and Workflow Automation: Orders are automatically assigned to the appropriate warehouse zones, ensuring that every order is processed efficiently and correctly.
The cumulative effect of these features is a substantial decrease in the number of picking and packing errors, leading to fewer returns and a smoother overall fulfillment process.
5. Improved Labor Productivity and Cost Efficiency
One of the most compelling benefits of adopting an advanced WMS is its impact on labor productivity. By automating routine tasks and optimizing workflows, companies can achieve:
- Enhanced Worker Productivity: Mobile applications and real-time guidance allow warehouse staff to complete tasks more quickly and accurately, reducing the need for extensive training and minimizing idle time.
- Lower Operational Costs: By processing more orders per employee, businesses can control labor costs even during peak periods. This is especially important when scaling operations without a proportional increase in workforce.
- Rapid Return on Investment: Many organizations report a significant ROI within the first 12 months after implementation, driven by cost savings, efficiency improvements, and increased throughput.
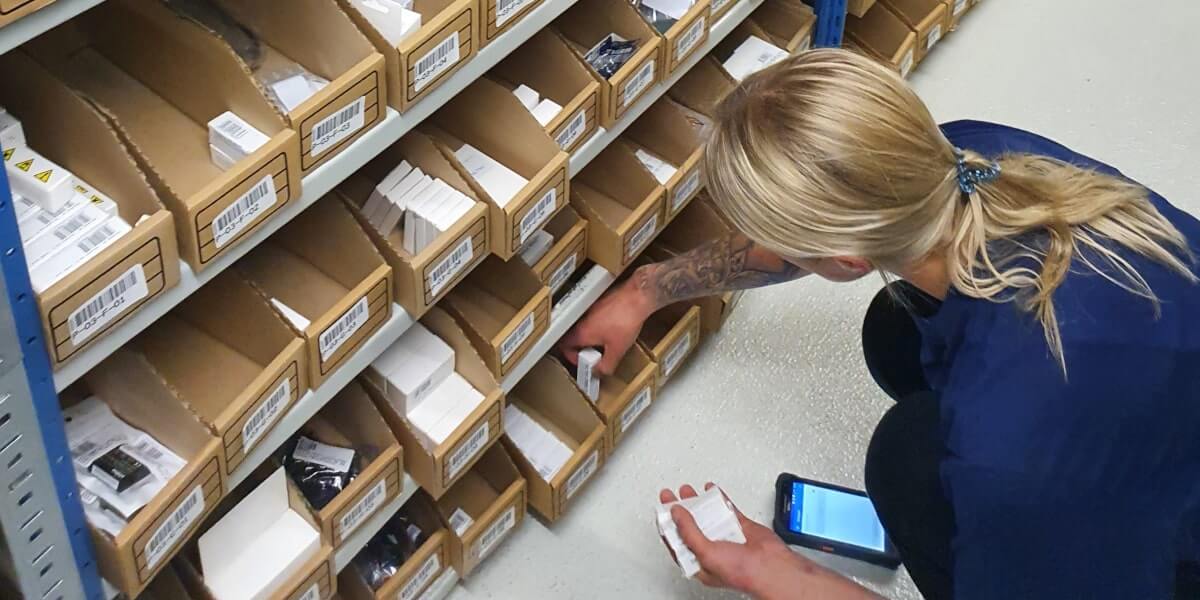
6. Comprehensive Reporting and Data-Driven Insights
Modern WMS solutions provide powerful reporting and analytics capabilities that enable managers to monitor, measure, and optimize warehouse operations. Key reporting features include:
- Real-Time Dashboards: Customizable dashboards offer immediate insights into key performance indicators such as order processing times, inventory turnover, and employee productivity.
- Custom Reports: Detailed, on-demand reports help identify inefficiencies and pinpoint opportunities for cost savings.
- Predictive Analytics: The connectivity of the WMS to Business Intelligence (BI) systems allows for the enrichment of data and enables warehouse managers to use proactive inventory management and strategic planning.
By leveraging these analytics tools, businesses can make informed decisions that enhance operational efficiency and drive continuous improvement.
Case study video: How a UK fashion retailer scaled up operations
In-depth look at key features of a leading Ecommerce WMS
To better understand how a modern WMS transforms warehouse operations, let’s explore several core features and how they contribute to operational excellence:
A. Enhancing Warehouse Efficiency with Automation and Smart Picking Strategies
An advanced Warehouse Management System (WMS) enhances efficiency by automating key warehouse operations and supporting flexible picking strategies. Key benefits include:
- Mobile Application Integration: Intuitive mobile interfaces enable quick training and efficient navigation for warehouse staff.
- Inbound Logistics Automation: Goods receipt and put-away are streamlined with automated data capture, reducing manual entry errors.
- Optimized Order Processing and Picking: Orders are automatically converted into pick lists, leveraging intelligent grouping and routing for efficient multi-order and batch picking.
- Automated Outbound Shipping: Shipping labels, tracking numbers, and carrier connections are generated automatically, ensuring timely dispatch.
B. Advanced Inventory Management
Effective inventory management is crucial to avoid stock discrepancies and ensure that customer orders are fulfilled accurately. Key aspects of advanced inventory management include:
- Real-Time Data Synchronization: Inventory levels are continuously updated across all channels, providing accurate and current stock information.
- Automated Replenishment: The system monitors inventory thresholds and automatically triggers replenishment orders when necessary, thereby preventing stockouts.
- Chaotic Storage Capabilities: By employing a dynamic storage method – often referred to as “chaotic warehousing” – the system maximizes the use of available space. Instead of assigning fixed locations to items, the system chooses the next available storage location, allowing for more flexible and efficient storage solutions.
C. Seamless Integration and Connectivity
A crucial requirement for any WMS is its ability to integrate seamlessly with existing systems. This includes connections to:
- Ecommerce Platforms: Whether it’s Shopify, Shopware, or another online platform, the WMS must be able to pull order data and update inventory in real time.
- ERP and Financial Systems: Integration with enterprise resource planning software ensures that financial data and order information remain synchronized across the business.
- Shipping and Carrier Networks: Automated connections with shipping carriers enable the rapid generation of labels, tracking of shipments, and seamless management of returns.
This interoperability ensures that all systems within the company work together harmoniously, creating a unified and efficient fulfillment ecosystem.
D. Robust Reporting and Business Intelligence
Data is at the heart of continuous improvement in warehouse operations. Advanced reporting capabilities provided by a modern WMS include:
- Customizable Dashboards: Managers can tailor dashboards to display the most relevant metrics, such as order processing speed, error rates, and inventory levels.
- Real-Time Alerts: Automated notifications can be set up to alert managers to any issues, such as low stock levels or order processing delays.
- Forecasting and Trend Analysis: By analyzing historical data, the system can forecast future demand and help plan inventory and staffing needs accordingly.
These features not only provide transparency but also enable proactive management and strategic decision-making.
Case study: How a WMS helped an Ecommerce brand scale efficiently
A European fashion retailer using Descartes pixi WMS experienced a 30% increase in fulfillment efficiency after implementation. By leveraging automated picking strategies and real-time inventory visibility, the company reduced order errors by 40%, leading to fewer returns and higher customer satisfaction.
Additionally, during their annual Black Friday campaign, the brand processed 5x more orders than the previous year without increasing warehouse staff, proving the scalability of an ecommerce WMS.
Key considerations when choosing an Ecommerce WMS
As businesses evaluate different warehouse management solutions, several critical factors should be considered:
Seamless System Integration
The ideal WMS must integrate flawlessly with the company’s existing technology stack. This includes not only the ecommerce platform but also ERP systems, financial software, and shipping networks. Look for solutions that offer robust APIs and standardized interfaces to ensure real-time data exchange and minimize errors.
Scalability to Meet Future Demands
A scalable system is essential for businesses expecting growth. Whether handling 300 orders a day or scaling up to tens of thousands, the solution should adapt seamlessly to changing demands. Cloud-based deployments often offer the best scalability, allowing companies to add capacity without significant upfront investment.
Automation and Efficiency Gains
Automation is at the heart of any modern WMS. Evaluate solutions based on their ability to automate key processes – from order receipt to picking, packing, and shipping. Features like mobile scanning, intelligent batching, and optimized routing are critical for reducing manual labor and minimizing errors.
Real-Time Visibility and Reporting
Access to real-time data is crucial for effective warehouse management. The chosen solution should provide customizable dashboards and reporting tools that offer insights into operational performance, inventory levels, and order processing times. These tools enable data-driven decision-making and continuous process improvement.
User-Friendly Interface and Fast Implementation
A steep learning curve can delay the benefits of a new system. The best solutions offer intuitive interfaces, streamlined workflows, and quick onboarding processes, often within a few weeks. Rapid implementation means that businesses can start reaping the benefits immediately, even during periods of high demand.
Comprehensive Support and Continuous Updates
Look for vendors that offer robust customer support, ongoing system updates, and a wide partner network. Continuous improvement and professional consultation are critical to ensure that the WMS evolves along with your business needs.
The broader impact: Enhancing customer satisfaction and business growth
Elevating the Customer Experience
Fast and accurate order fulfillment directly contributes to customer satisfaction. An advanced WMS can:
- Reduce Order Errors: Automation minimizes picking and packing mistakes, leading to fewer returns and exchanges.
- Ensure Timely Deliveries: Optimized workflows and real-time processing enable same-day shipping, even during demand spikes.
- Enhance Communication: Automated notifications keep customers informed of order status and shipping updates, building trust and transparency.
Unlocking Profitability
Streamlined warehouse operations translate directly into cost savings and improved productivity. Key benefits include:
- Labor Cost Savings: By reducing the need for manual intervention, companies can maintain high throughput without proportionally increasing staffing.
- Higher Throughput: More orders processed per employee translate to faster order turnaround and greater overall capacity.
- Better ROI: The efficiency gains and cost savings typically result in a return on investment within the first year of implementation.
Conclusion: Transforming warehouse logistics into a strategic asset
Investing in an advanced ecommerce WMS like Descartes pixi, is no longer a luxury for fast-growing D2C brands and online retailers – it is a strategic imperative. By automating and optimizing every aspect of the fulfillment process, companies can overcome the challenges of fluctuating order volumes, complex inventory management, and high labor costs. This digital transformation enables businesses to not only improve operational efficiency but also elevates the customer experience, paving the way for sustainable growth and international expansion.
Final thoughts
In an industry where every minute counts and customer expectations are constantly rising, transforming your warehouse logistics through a digital WMS is not merely about staying competitive – it’s about setting new standards for efficiency, accuracy, and growth. By leveraging an advanced system that integrates automation, real-time analytics, and seamless connectivity, fast-growing D2C brands and ecommerce retailers can turn potential pain points into powerful strategic advantages.
Choosing the right system – and ensuring it is implemented effectively – will ultimately determine your ability to meet market demands, delight your customers, and achieve sustainable growth.
Embrace the digital transformation in warehouse management today and empower your business to thrive in tomorrow’s competitive ecommerce landscape.
Author: Johannes Panzer, Head of Industry Solutions for Ecommerce at Descartes.
Vita: With 17 years in ecommerce fulfillment and shipping in B2B and SaaS, Johannes Panzer drives the go-to-market strategy for Descartes’ ecommerce division globally. He leads the ecommerce industry strategy group, managing SMEs’ software solutions, including Peoplevox, pixi, ShipRush and Ozlink.
***